十点法
「十点法」という言い方をご存知だろうか.
あまりいい名前ではないが,部品の定量投入によるポカよけの一種である.
例えばネジ締め作業で必要なネジの数だけ作業前に取り置き,作業が終わったときにネジを過不足なく使用したことを確認するわけである.これによりネジの閉め忘れとか,製品の中への落下などを防止するわけである.
すなわち10点部品を使うならば,10個の部品を投入するという意味の命名である.
中国の工場で指導をしていた時に,製品組立工程でネジを5本締め付ける工程があった.このとき現場の組長さんに「このネジが一本足りなくなったらどうする?」と聞いてみた.
この若い組長さんは大変聡明な人ですぐに小皿を持ってきて,作業者に作業前にネジを必要数準備してから作業をするよう指示をしていた.
普通の組長さんだと,次の工程にネジの数を数える検査を追加したりする.
この方法でもネジの締め忘れがないことを保証できるかもしれないが,製品の中にネジが落下したのは検査できない.
それよりも,付加価値を生まない作業を増やしていることになる.
検査を追加することよりも,作業で品質を保証する仕組みを考えるべきだ.
製品に貼り付けるラベルを貼り忘れ,出荷先で見つかってしまった事がある.
この手の不良は厄介である.客先に出荷してしまった製品の選別検査,社内の完成品の再検査など,後向きの作業が大量に発生する.
客先にも改善対策を提示しなければならない.当然工程内には外観検査があり,ラベルが貼ってあることも検査している.作業者がうっかり貼り忘れ,検査者もうっかり見逃したわけである.
ついうっかりの二乗なので,確率はかなり低いはずであるが往々にしてこういう事故はある.
殆ど不良が発生しないと,検査者の感度は落ちてしまうのであろう.
こういうときに「十点法」が活用できる.
ラベルを梱包単位に準備し,ラベルを使い切ったらラベルシールの台紙をベルトコンベアに載せる.梱包作業者はラベルシールの台紙が流れてきたら,梱包箱が一箱完成しているのを確認する.
ラベルを貼りそこなった場合の対処方法など,一工夫する必要はあるが,この方法はそれほど工数をかけずに,ラベルの貼り忘れがないことを保証できる.
同時に梱包数量の確認も出来ている.
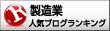
あまりいい名前ではないが,部品の定量投入によるポカよけの一種である.
例えばネジ締め作業で必要なネジの数だけ作業前に取り置き,作業が終わったときにネジを過不足なく使用したことを確認するわけである.これによりネジの閉め忘れとか,製品の中への落下などを防止するわけである.
すなわち10点部品を使うならば,10個の部品を投入するという意味の命名である.
中国の工場で指導をしていた時に,製品組立工程でネジを5本締め付ける工程があった.このとき現場の組長さんに「このネジが一本足りなくなったらどうする?」と聞いてみた.
この若い組長さんは大変聡明な人ですぐに小皿を持ってきて,作業者に作業前にネジを必要数準備してから作業をするよう指示をしていた.
普通の組長さんだと,次の工程にネジの数を数える検査を追加したりする.
この方法でもネジの締め忘れがないことを保証できるかもしれないが,製品の中にネジが落下したのは検査できない.
それよりも,付加価値を生まない作業を増やしていることになる.
検査を追加することよりも,作業で品質を保証する仕組みを考えるべきだ.
製品に貼り付けるラベルを貼り忘れ,出荷先で見つかってしまった事がある.
この手の不良は厄介である.客先に出荷してしまった製品の選別検査,社内の完成品の再検査など,後向きの作業が大量に発生する.
客先にも改善対策を提示しなければならない.当然工程内には外観検査があり,ラベルが貼ってあることも検査している.作業者がうっかり貼り忘れ,検査者もうっかり見逃したわけである.
ついうっかりの二乗なので,確率はかなり低いはずであるが往々にしてこういう事故はある.
殆ど不良が発生しないと,検査者の感度は落ちてしまうのであろう.
こういうときに「十点法」が活用できる.
ラベルを梱包単位に準備し,ラベルを使い切ったらラベルシールの台紙をベルトコンベアに載せる.梱包作業者はラベルシールの台紙が流れてきたら,梱包箱が一箱完成しているのを確認する.
ラベルを貼りそこなった場合の対処方法など,一工夫する必要はあるが,この方法はそれほど工数をかけずに,ラベルの貼り忘れがないことを保証できる.
同時に梱包数量の確認も出来ている.
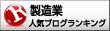
本当の改善力
日本のモノ造りの力は「改善力」にあると考えている.
徹底的に工程内不良を減らし直行率を上げる.
こういう改善力が日本のモノ造りの力だ.
1990年代初頭にシンガポールのハードディスク組立工場を訪問した事がある.
ラインを見せていただき,工程内不良が多いように感じた.工場を案内してくれた幹部に聞くと,直行率が80%を上回ったらもう改善しない,と言っていた.改善にかけるリソースを新機種のライン立ち上げに振り向ける,と言うのだ.
次々と容量の大きな新機種がリリースされる業界だ.旧機種はすぐさま値崩れをして利益を確保できなくなる.一見合理的な考えのように聞こえる.
しかし改善力を磨かなければ,次に立ち上げた新機種も低い直行率からのスタートとなる.
製品の生産ライフが短くなればなるほど,その影響は大きい.
それから20年近く経った中国の生産現場では,最新鋭の機械設備で生産している中国企業はいくらでもある.日本のモノ造りをまね,実力もつけてきた.
「トヨタ生産方式」を売り物にしている中国人コンサルタントもいる.
また長年日本の生産現場で活躍してきた人材を雇い入れている中国企業も多い.
では日系の工場はもう優位性がないのかと言うと,そうではない.
まだまだ日本のモノ造りのココロの有意性はあると考えている.
本当の日本の「改善力」は,
徹底的に工程内不良を減らし直行率を上げる.
こういう改善力が日本のモノ造りの力だ.
1990年代初頭にシンガポールのハードディスク組立工場を訪問した事がある.
ラインを見せていただき,工程内不良が多いように感じた.工場を案内してくれた幹部に聞くと,直行率が80%を上回ったらもう改善しない,と言っていた.改善にかけるリソースを新機種のライン立ち上げに振り向ける,と言うのだ.
次々と容量の大きな新機種がリリースされる業界だ.旧機種はすぐさま値崩れをして利益を確保できなくなる.一見合理的な考えのように聞こえる.
しかし改善力を磨かなければ,次に立ち上げた新機種も低い直行率からのスタートとなる.
製品の生産ライフが短くなればなるほど,その影響は大きい.
それから20年近く経った中国の生産現場では,最新鋭の機械設備で生産している中国企業はいくらでもある.日本のモノ造りをまね,実力もつけてきた.
「トヨタ生産方式」を売り物にしている中国人コンサルタントもいる.
また長年日本の生産現場で活躍してきた人材を雇い入れている中国企業も多い.
では日系の工場はもう優位性がないのかと言うと,そうではない.
まだまだ日本のモノ造りのココロの有意性はあると考えている.
本当の日本の「改善力」は,
改善を継続する力
現場の改善力
にある.
優秀な人材を雇い入れ改善プロジェクトを起こす.目標に達したら,改善プロジェクトをやめる.
こういう合理主義的改善では,現場が日々改善を続ける改善力は得られない.
日本の最新鋭の生産設備を導入する.
トヨタ方式を導入する.
セル生産方式を導入する.
このような方法で,日本のモノ造りの強さを真似できるかもしれない.
しかし本当の日本のモノ造りの強さは,表面的なところにはない.日々改善する現場の力は,企業文化によって支えられており,その本当の力は表面からは見えない.簡単には真似をすることができないはずだ.
改善のPDCA
よく改善のPDCAを回せという.
改善を継続させるという意味で言うことが多い.
そのPDCAとは以下の意味だ.
P,D,Cまではこのままで分かるはずだが,「A:アクション」がよく分かっていないのではないかと思っている.
何をするのがアクションなのか?Doとは何が違うのかを理解しなければならない.
こんな風に説明すれば分かりやすいと思っている.
A=F+S+V
つまりアクションの中身は
改善を実施したらそこで終わりではない.
その改善がうまく行っているかどうかきちんとフォローする.
その改善が維持されるように標準化をする.
その改善の効果を評価する.
これらのステップを入れた後に次のPDCAにつなげてゆくのだ.
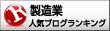
改善を継続させるという意味で言うことが多い.
そのPDCAとは以下の意味だ.
P:Plan,計画.何をいつまでにどれだけ改善するか目標を立てる.
D:Do,実施.改善案を考え実施する.
C:Check,チェック.改善の効果を確認する.
A;Action,アクション.
P,D,Cまではこのままで分かるはずだが,「A:アクション」がよく分かっていないのではないかと思っている.
何をするのがアクションなのか?Doとは何が違うのかを理解しなければならない.
こんな風に説明すれば分かりやすいと思っている.
A=F+S+V
つまりアクションの中身は
F:フォロー
S:標準化
V:評価
改善を実施したらそこで終わりではない.
その改善がうまく行っているかどうかきちんとフォローする.
その改善が維持されるように標準化をする.
その改善の効果を評価する.
これらのステップを入れた後に次のPDCAにつなげてゆくのだ.
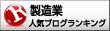
「瞬間」を見る
改善の第一歩は「瞬間」を見ることだと考えている.
加工の「瞬間」を見る.
不具合が発生する「瞬間」を見る.
こういう「瞬間」が見えれば改善はうまく行く.
モノ造りをしていると機械化がうまく行かず,どうしても作業員の熟練によらざるを得ない工程がある.
ある工場で製品にテープを貼り付ける工程があった.幅5mm程のテープを台紙から剥がして製品に貼り付ける.ただそれだけの作業なのだが,作業者によって上手い,下手が際立ってしまう.
この工程がネックになってしまい,現場を指導している監督者が頭を抱えている.
こういう作業は作業者の動作をじっと観察することだ.
上手い作業者と下手な作業者の上手い・下手を分ける瞬間を見つけることだ.
この作業をよく観察してみると,台紙から剥がしたテープが静電気で帯電しており作業者の指に吸着していることが分かった.
右手で持ったピンセットでテープを台紙から剥がす.このときにテープは剥離帯電している.作業者がテープの端をつかもうと指を近づけたときに,帯電したテープが指に絡みつき上手くテープをつかめない.そのためテープをまっすぐに伸ばしなおす無駄な作業が発生する.テープの粘着部分がくっつきあって使えなくなれば,初めから作業のやり直しである.
上手い作業者をよく観察していると,テープをつかみに行かない.人差し指を僅かにテープに近づけるだけで,テープの方が指の方に静電気で吸い付いてくる.これを待ってそっとつかんでいる.
作業者は理屈は分かっていなくても,何度も同じ作業を繰り返すうちに体でコツを覚えている.
こういうコツを見つけ出し,その原理を解明する.コツを言語化して他の作業員にも教える.
こういうことができなければ現場の改善はできない.
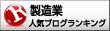
加工の「瞬間」を見る.
不具合が発生する「瞬間」を見る.
こういう「瞬間」が見えれば改善はうまく行く.
モノ造りをしていると機械化がうまく行かず,どうしても作業員の熟練によらざるを得ない工程がある.
ある工場で製品にテープを貼り付ける工程があった.幅5mm程のテープを台紙から剥がして製品に貼り付ける.ただそれだけの作業なのだが,作業者によって上手い,下手が際立ってしまう.
この工程がネックになってしまい,現場を指導している監督者が頭を抱えている.
こういう作業は作業者の動作をじっと観察することだ.
上手い作業者と下手な作業者の上手い・下手を分ける瞬間を見つけることだ.
この作業をよく観察してみると,台紙から剥がしたテープが静電気で帯電しており作業者の指に吸着していることが分かった.
右手で持ったピンセットでテープを台紙から剥がす.このときにテープは剥離帯電している.作業者がテープの端をつかもうと指を近づけたときに,帯電したテープが指に絡みつき上手くテープをつかめない.そのためテープをまっすぐに伸ばしなおす無駄な作業が発生する.テープの粘着部分がくっつきあって使えなくなれば,初めから作業のやり直しである.
上手い作業者をよく観察していると,テープをつかみに行かない.人差し指を僅かにテープに近づけるだけで,テープの方が指の方に静電気で吸い付いてくる.これを待ってそっとつかんでいる.
作業者は理屈は分かっていなくても,何度も同じ作業を繰り返すうちに体でコツを覚えている.
こういうコツを見つけ出し,その原理を解明する.コツを言語化して他の作業員にも教える.
こういうことができなければ現場の改善はできない.
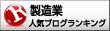