改善指標
金属部品加工工場のお客様で実施した,QCC活動の実践研修の事例をご紹介しよう.
11サークルのメンバーに,課題設定から発表までを,実際に活動する形で指導した.
活動のQCステップごとに講義・演習をし,次の回までに各サークルの実テーマをそのステップまで完了し,サークルごとに発表をしてもらっている.
ひとつのサークルは「ロット不良の低減」をテーマに取り組んでいる.彼らの原因分析ステップの発表を聞いても,全く理解できない.こういう場合は,研修室を出てすぐ現場に行くことにしている.
4月にロット不良が44件もあった.これを8件までに減らす目標を立てている.
しかしその原因解析が,要領を得ない.
現場で分かったコトは,このサークルは製造部門のサークルではなく,IPQC(工程内品質管理)部門のサークルである.彼らが発見するロット不良を,減らしたいと言うテーマだ.
製造部ならばロット不良を減らすことが目標となるのは分かるが,IPQCがなぜロット不良低減を目標としているのか理解が出来ない.
IPQCはたくさん不良ロットを見つけるのが成果だ.ロット不良を減らすのは目標にならない.
理解不能の原因はこの工場のロット不良の定義にあった.
この工場では,自動生産設備が生産している部品を,2時間に一回10個抜き取り検査を行い,不良が見つかるとロットアウトとして廃棄処分をする.
しかし彼らはそれをロット不良としてカウントしない.2時間以内に見つけられなかった場合をロット不良として定義している.
IPQC検査員は12台の設備を巡回しながら,抜き取り検査をしている.従って一回の検査を10分以内に完了しないと,12台の設備の抜き取り検査に2時間以上かかってしまう.この時不良を見つけると,ロット不良となる.
考え方としては,IPQCが不良を適時に発見した場合はロット不良としない(製品は廃棄)ということだ.製造部や,設備メンテナンスの部門にとって明らかにロット不良であるが,IPQCがその損失を最小限に抑えたのだから,大目に見るということだろう.
これで全てが見えた.
彼らの活動は,ロット不良を減らす,という品質改善のテーマでは無い.
2時間以内に12台の設備の抜き取り検査を終わるようにする,という作業改善のテーマなのだ.
改善指標は(正しい意味の)ロット不良の低減ではなく,抜き取り検査時間の短縮,なのだ.
ならば話が早い.
現場でIPQC検査員の作業を観察すると,二次元投影測定器の操作に個人差があるのが分かる.これを改善すれば良いのだ.特定のIPQC検査員が出来ていないだけなので,この改善で2時間以内は全員が達成できるだろう.
しかし2時間に一回抜き取り検査というのは,自分たちの都合で決めた決まりだ.もし1時間に1回抜き取り検査をすれば,不良損失は半分になる.
本来不良をなくすのが改善だが,IPQCのメンバーにとっては検査時間を半分にするのが改善のはずだ.
こういう話を現場のリーダにすると即座に「不可能!」と答えが返って来た.
それは今の方法でやっているから,不可能なだけだ.方法を変えれば,可能となる.
その方法を教えたいのは山々だが,ぐっとこらえる(笑)
まず2時間以内をIPQC検査員全員が実現することで,達成感を持ってもらう.
その次の課題として「検査時間半分=損失半減」と言う改善に取り組んでもらうことが出来ればと考えている.
ところでこの事例のように,製造部とIPQCで正反対の目標(つまり,一方はたくさん良品を造る.他方はたくさん不良を見つける)を持っている場合,適切にその指標を決めてやらなければならない.
正しい意味でロット不良を減らすことは製造部にとっては,努力しなければならない目標だが,IPQCが同じ目標を達成しようとすれば,検査をしなければ良いのだ.一方IPQCが不良を見逃せば,製造部は何の努力も無く改善できた様に見える.
今回の事例では,IPQCの指標を「不良適時発見による損失コストの削減」とし,廃棄しなければならなくなった製品が何時間分(少ない方が良い)とするのが良かろう.
こうすれば製造部は品質を改善してロット不良を減らす.
IPQCは作業改善をして,短時間で抜き取り検査を完了することにより,不良を造り続ける時間を減らす.当面は利害が一致するはずだ.
「当面は」と書いたのは,本来は設備を改善して不良を作らなくする,生産中に良品・不良品の判定機能を付加し,不良が発生したら停止する(人偏のある自働化)というのが本質的改善だからだ.
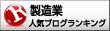
11サークルのメンバーに,課題設定から発表までを,実際に活動する形で指導した.
活動のQCステップごとに講義・演習をし,次の回までに各サークルの実テーマをそのステップまで完了し,サークルごとに発表をしてもらっている.
ひとつのサークルは「ロット不良の低減」をテーマに取り組んでいる.彼らの原因分析ステップの発表を聞いても,全く理解できない.こういう場合は,研修室を出てすぐ現場に行くことにしている.
4月にロット不良が44件もあった.これを8件までに減らす目標を立てている.
しかしその原因解析が,要領を得ない.
現場で分かったコトは,このサークルは製造部門のサークルではなく,IPQC(工程内品質管理)部門のサークルである.彼らが発見するロット不良を,減らしたいと言うテーマだ.
製造部ならばロット不良を減らすことが目標となるのは分かるが,IPQCがなぜロット不良低減を目標としているのか理解が出来ない.
IPQCはたくさん不良ロットを見つけるのが成果だ.ロット不良を減らすのは目標にならない.
理解不能の原因はこの工場のロット不良の定義にあった.
この工場では,自動生産設備が生産している部品を,2時間に一回10個抜き取り検査を行い,不良が見つかるとロットアウトとして廃棄処分をする.
しかし彼らはそれをロット不良としてカウントしない.2時間以内に見つけられなかった場合をロット不良として定義している.
IPQC検査員は12台の設備を巡回しながら,抜き取り検査をしている.従って一回の検査を10分以内に完了しないと,12台の設備の抜き取り検査に2時間以上かかってしまう.この時不良を見つけると,ロット不良となる.
考え方としては,IPQCが不良を適時に発見した場合はロット不良としない(製品は廃棄)ということだ.製造部や,設備メンテナンスの部門にとって明らかにロット不良であるが,IPQCがその損失を最小限に抑えたのだから,大目に見るということだろう.
これで全てが見えた.
彼らの活動は,ロット不良を減らす,という品質改善のテーマでは無い.
2時間以内に12台の設備の抜き取り検査を終わるようにする,という作業改善のテーマなのだ.
改善指標は(正しい意味の)ロット不良の低減ではなく,抜き取り検査時間の短縮,なのだ.
ならば話が早い.
現場でIPQC検査員の作業を観察すると,二次元投影測定器の操作に個人差があるのが分かる.これを改善すれば良いのだ.特定のIPQC検査員が出来ていないだけなので,この改善で2時間以内は全員が達成できるだろう.
しかし2時間に一回抜き取り検査というのは,自分たちの都合で決めた決まりだ.もし1時間に1回抜き取り検査をすれば,不良損失は半分になる.
本来不良をなくすのが改善だが,IPQCのメンバーにとっては検査時間を半分にするのが改善のはずだ.
こういう話を現場のリーダにすると即座に「不可能!」と答えが返って来た.
それは今の方法でやっているから,不可能なだけだ.方法を変えれば,可能となる.
その方法を教えたいのは山々だが,ぐっとこらえる(笑)
まず2時間以内をIPQC検査員全員が実現することで,達成感を持ってもらう.
その次の課題として「検査時間半分=損失半減」と言う改善に取り組んでもらうことが出来ればと考えている.
ところでこの事例のように,製造部とIPQCで正反対の目標(つまり,一方はたくさん良品を造る.他方はたくさん不良を見つける)を持っている場合,適切にその指標を決めてやらなければならない.
正しい意味でロット不良を減らすことは製造部にとっては,努力しなければならない目標だが,IPQCが同じ目標を達成しようとすれば,検査をしなければ良いのだ.一方IPQCが不良を見逃せば,製造部は何の努力も無く改善できた様に見える.
今回の事例では,IPQCの指標を「不良適時発見による損失コストの削減」とし,廃棄しなければならなくなった製品が何時間分(少ない方が良い)とするのが良かろう.
こうすれば製造部は品質を改善してロット不良を減らす.
IPQCは作業改善をして,短時間で抜き取り検査を完了することにより,不良を造り続ける時間を減らす.当面は利害が一致するはずだ.
「当面は」と書いたのは,本来は設備を改善して不良を作らなくする,生産中に良品・不良品の判定機能を付加し,不良が発生したら停止する(人偏のある自働化)というのが本質的改善だからだ.
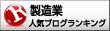