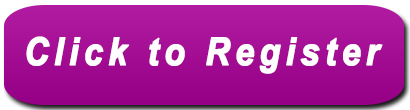
- 18v DC Motor Drill RS-550 D-Shaft 1/8in / 3.175mm Shaft.
- Position and Speed Control of Brushless DC Motors Using.
- DC Motor Speed and Direction Control with L293D Driver IC and Arduino.
- PDF DC Motor Troubleshooting - Hackspace.
- BLDC Motor Controller: Design Principles & Circuit Examples.
- Controlling DC Motors Using Python With a Raspberry Pi.
- DC Motor: Split rings vs commutator - Physics Stack Exchange.
- DC motor needs help to start rotating - Arduino Forum.
- How To Control a DC Motor with an Arduino - Projects.
- Controlling A DC Motor With Arduino - BC Robotics.
- How to Control a DC Motor (Or Motors) Using Your Raspberry Pi.
- Things to Do in Chicago - Chicago Tribune.
- DC Training: The Ultimate Guide! - Revolutionary Program Design.
- Advantages of DC motors in industrial applications.
18v DC Motor Drill RS-550 D-Shaft 1/8in / 3.175mm Shaft.
LaTeX Tutorial provides step-by-step lessons to learn how to use LaTeX in no time. It allows you to start creating beautiful documents for your reports, books and papers through easy and simple tutorials.
Position and Speed Control of Brushless DC Motors Using.
I need to run a couple of stepper motors at 800 - 1000 rpm. There will not be much load on them, they just need to spin at high RPM My initial questions are... 1) which stepper drive can support at least 24v and possibly up 80v which I think may be necessary for high rpm. 2) I know very little about steppers so any recommendations on which models to look at would be great. Apr 01, 2019 · Depending on the needs of your application, the brushed DC motor might be the more suitable option. If a simple control scheme and low cost is your primary concern, consider the use of a brushed DC motor. Brushless DC Motors. Brushless DC Motor (Ref: ISL Products) Brushless DC motors are mechanically simpler than brushed ones.
DC Motor Speed and Direction Control with L293D Driver IC and Arduino.
12v battery/car starter motor and a solenoid. the solenoid is simply switched on/off to control the lure. there is not much load on the starter, it is fitted with a plastic spool which holds the line for the lure, the lure is also very light. I would like to ask the best way to accurately control the speed of the motor as the current method. Shunt Wound DC Motor. When dc voltage V is applied across the motor terminals, the field magnets are excited and armature conductors are supplied with current. Therefore, driving torque acts on the armature which begins to rotate. As the armature rotates, back emf Eb is induced which opposes the applied voltage V. The applied voltage V has to force current through the armature against the back.
PDF DC Motor Troubleshooting - Hackspace.
The 6 volt solenoid is fine, because when I attempt to start the car using the starter button, the solenoid will engage the bendix spring and turn the moter over, however slow. I'm thinking that I can get away with using this 12 volt start for now rather than try to convert the whole system to 12 volt, which I don't really want to do.
BLDC Motor Controller: Design Principles & Circuit Examples.
Practical DC motors is that DC motors rotate rather than move in a straight line. The same forces that cause a linear motor to move "right or left" in a straight line cause the DC motor to rotate. This chapter will examine how the linear motor principles can be used to make a practical DC motor spin. 16.1 Electrical machinery. 2012-04-10 12:24 am. #1. Application: 12-24v DC motor with gear-head needed for smooth and silent operation of a vibraphone mechanism, Ideally 20-200rpm. Problem: replacement "vibraphone motor with controller" can retail for over $700! I'm finding some good deals on ebay but need some direction on which motor and controller to buy. Sometimes a combination of an induction motor for washing with a brushed motor for the high rpm of the spin cycle (up to 1400 rpm at the drum, so at least 15000rpm for the motor.
Controlling DC Motors Using Python With a Raspberry Pi.
Step 1. Check the power. If you suspect the fan motor is bad, the first thing you should check is the power to the motor and the power to the air conditioning unit. Locate the circuit breaker and ensure it hasn't tripped. If the power is fine, check to see if there is proper voltage. The numbers 16, 18 and 22 we will use to tell Python they are the pins associated with the motors. When using the L293D you can give it a direction, by turning one side on to turn in one direction, called pin A and vice versa is pin B. To turn the motor on use a pin called Enable, labelled E in the test script-this is pin 22. 18v DC Motor Drill RS-550 D-Shaft 1/8in / 3.175mm Shaft - Fan Cooled High Torque 20K RPM Power Tool Replacement Upgrade 18 Volt (12v - 24v DC) DIY Electric Projects Robots Remote Controlled Car: A Tools & Home Improvement.
DC Motor: Split rings vs commutator - Physics Stack Exchange.
I am trying to control a dc motor with an SN754410 h bridge. When connected directly to the battery (9V, voltage read w/ multi meter ~8.1V) it starts running immediately at a relatively high speed. However, when I connect it through the h bridge, it makes a buzzing noise and will only start rotating if I physically twist the shaft with my fingers first. If I measure the voltage delivered to. 2 Answers. I think you are both right! With a slip ring it becomes an AC motor, and it will not run on DC. This is no different to a coil connected to a power supply without any sort of commutator being used. All depends on the initial orientation of the plane of the coil relative to the magnetic field.
DC motor needs help to start rotating - Arduino Forum.
If your AC offers different fan settings, check if it is set at low speed. If that isn't the case, it could mean the motor bearings need to be oiled or that the capacitor is failing. 4. The fan runs intermittently. When the fan runs intermittently, it could be one of two problems. Control the direction of the spin of DC motor Components Required You will need the following components − 1x Arduino UNO board 1x PN2222 Transistor 1x Small 6V DC Motor 1x 1N4001 diode 1x 270 Ω Resistor Procedure Follow the circuit diagram and make the connections as shown in the image given below. Precautions.
How To Control a DC Motor with an Arduino - Projects.
Weeks 18-20: 5-Way Split; This is just a hypothetical example of how your progression might look. If you can use the 2-way split for your entire diet then use that! The 3-way and 5-way splits are just options you have if the 2-way is really starting to kick your ass. Part 12: Advanced DC Training: Overview. The inboard boat motor firm of Caille Motor Company of Detroit were instrumental in making the cylinder and engines. The most successful early outboard motor, was created by Norwegian-American inventor Ole Evinrude in 1909. Between 1909 and 1912, Evinrude made thousands of his outboards and the three-horsepower units were sold around the world.
Controlling A DC Motor With Arduino - BC Robotics.
The power of a motor is the product of its speed and torque. The power output is greatest at about half way between the unloaded speed (maximum speed, no torque) and the stalled state (maximum torque, no speed). The output power in watts is about (torque) x (rpm) / 9.57. To connect a DC motor to a circuit simply so that it will spin is very easy. All you have to do is connect the amount of DC voltage to the motor which it is rated for. Therefore, for a DC motor rated at 9 volts, all you must do is connect 9V to the circuit. Below is a Nichibo PC-280P DC motor, which operates on 3-18VDC.
How to Control a DC Motor (Or Motors) Using Your Raspberry Pi.
A battery with a 1600 mAh rating will provide 1 mA for close to 1600 hours, however, it will not provide 1.6A for a full hour. Consider adding a second battery in parallel, this will keep the supply voltage the same but increase the capacity. Laptop batteries commonly use 4 cells in series to increase the voltage, and two parallel sets of the 4. Slide it off the battery and then pull one end through the coil and wrap it around once to hold that end in place. Carefully look at the coil and wrap the other loose end on the exact opposite side of the coil. They need to be centered opposite from each other so they balance each other. Try to straighten both sides.
Things to Do in Chicago - Chicago Tribune.
With the MotorControl sketch uploaded, click the serial monitor button at the top right of your Arduino window. The serial monitor window will show you the potentiometer value followed by the output value that is being sent to the motor, in this fashion: potentiometer = 1023 motor = 255. These values are displayed in a long list and update as. A common electric bicycle setup is a 36V (volt) battery and a 15A (amp) controller. Wattage is just voltage multiplied by current, so 36 volts x 15 amps = 540 watts. In this case, we are looking at an ebike of approximately 500 watts. Do the math just like this on any electric bicycle to determine just how much power that specific ebike is. May 25, 2020 · The SC-E8000 Wireless Cycle Computer display shows basic info like reach or cadence and comes in color, the SC-E7000 version comes with a black and white display.
DC Training: The Ultimate Guide! - Revolutionary Program Design.
A sensorless BLDC motor makes use of the electromotive force (EMF) that gives rise to a current in the windings of any DC motor with a magnetic field that opposes the original change in magnetic flux as described by Lenz's Law. The EMF tends to resist the rotation of the motor and is therefore referred to as "back" EMF. A brushed DC electric motor is an internally commutated electric motor designed to be run from a direct current power source and utilizing an electric brush for contact.. Brushed motors were the first commercially important application of electric power to driving mechanical energy, and DC distribution systems were used for more than 100 years to operate motors in commercial and industrial.
Advantages of DC motors in industrial applications.
Introduction. The history of the first brushless DC (BLDC) motor dates back to 1962. The implementation of this new type of electrical motor was made possible thanks to a transistor switch invented shortly before. Using electronics instead of a mechanical commutator with brushes was a breakthrough in electrical engineering at that time. A simple method would be to time how long it takes your motors to make the valves go from open to fully closed. Then add 30-50% to this time and reduce the current to the motor after the timer expires. Should be fairly easy to do if you are using a micro controller to activate the motors and would require no extra hardware to PWM them. It takes a certain amount of current to get the motor to start. It is called the stall current. It may very well be that it takes that PWM value to supply the required current to the motor to start it. Post a data sheet for the motor. The L298 is ancient and inefficient technology.
See also:
Gta V 10Th Casino Card Location
Michael Biehn Pistol Spinning Technique
Falcon Raceway Digital Slot Carclub
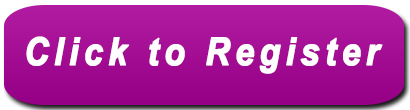